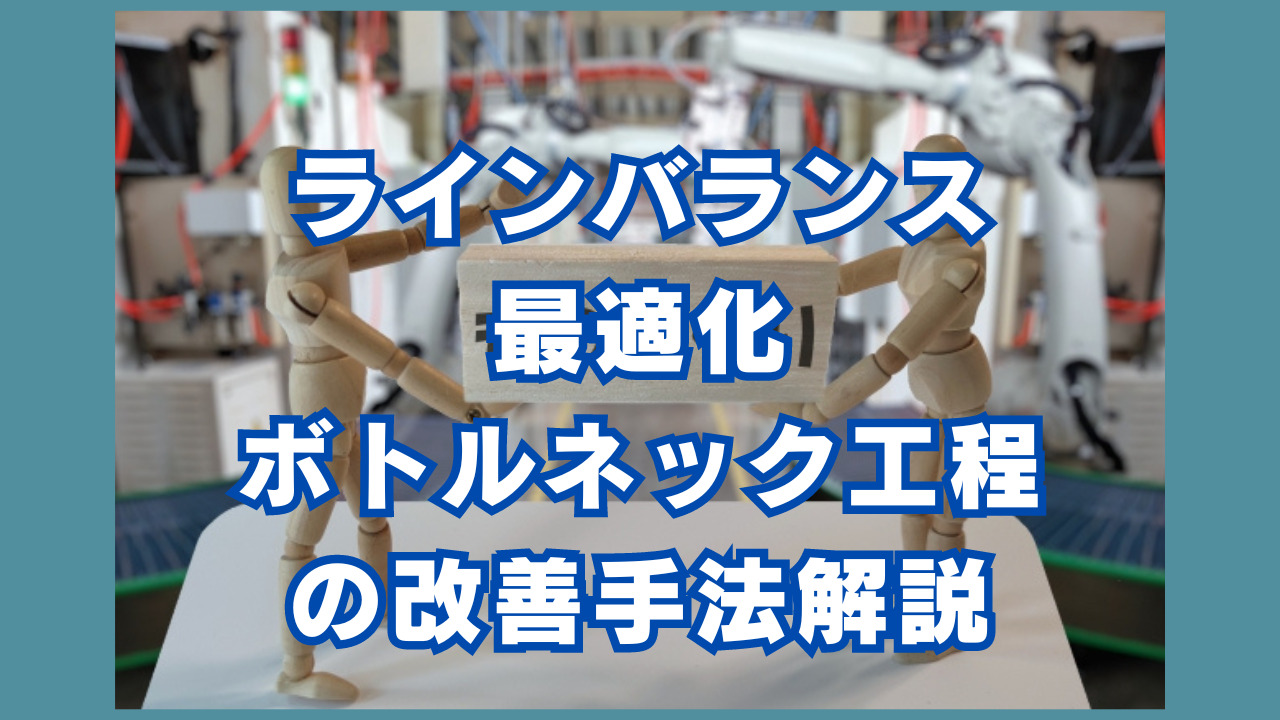
製造業における生産効率の向上は、企業の競争力を左右する重要な要素です。特に、自動車産業では、ラインバランスとボトルネック工程の改善が鍵となります。本記事では、ラインバランスの基本からボトルネック工程の特定方法、具体的な改善手法までを詳しく解説します。
品質マネジメントシステム普及の応援が目的のサイトです!「難解な規格を簡単に解説」をモットーに、「ちょっと相談したい」ときに頼りになるコンサルタントを目指しています!まずはお気軽にご連絡ください★
「無料で学ぶ」「有料で実践する」——皆様の目的に合わせて活用可能です!
✅ QMS・品質管理・製造ノウハウを無料で学びたい方へ
👉 本サイト「QMS学習支援サイト」を活用しましょう!「QMSについて知りたい」「品質管理の基礎を学びたい」方に最適!
✔ IATF 16949やISO 9001・VDA6.3の基礎を学ぶ
✔ 品質管理や製造ノウハウを無料で読む
✔ 実務に役立つ情報を定期的にチェック
✅ 実践的なツールやサポートが欲しい方へ
👉 姉妹サイト「QMS認証パートナー」では、実務で使える有料のサポートサービスを提供!「すぐに使える資料が欲しい」「専門家のサポートが必要」な方に最適!
✔ コンサルティングで具体的な課題を解決
✔ すぐに使える帳票や規定のサンプルを購入
✔ より実践的な学習教材でスキルアップ
皆様の目的に合わせて活用可能です!
・当サイトの内容は、あくまでもコンサルタントとして経験による見解です。そのため、保証するものではございません。 ・各規格の原文はありません。また、規格番号や題目なども当社の解釈です。 ・各規格については、規格公式サイトを必ず確認してください。 ・メールコンサルティングは空きあります(2025年6月現在)。この機会に「ちょっと相談」してみませんか?1週間の無料サービス期間を是非ご利用ください。 →サービスのお問い合わせはこちら |
2025年:新企画始動告知!
メールコンサルティング初回契約:初月50%以上割引★
サービス詳細はこちら
・オンラインコンサル/現地コンサルの空き状況について
【現在の空き状況:2025年6月現在】
・平日:6時間以上ご利用で月1回のみ
・夜間:19:30-21:00でご相談承ります
・土日:少々空きあります
オンライン会議システムを利用したコンサル詳細はこちら
IATF16949の構築・運用のコツは「規格の理解」と「ルールと記録の構築」の2つがカギ!ISO9001とのギャップを埋める教材とサンプルを利用しつつ、相談しながら低コストで対応可能なノウハウをご提供いたします!
【IATF16949:おすすめ教材】
👑 | 教材No. | タイトル:詳細はこちら |
1 | No.1-001 | IATF16949+ISO9001学習教材 |
2 | No.2-001 | コアツール学習教材 |
3 | No.7-001 | IATF16949_内部監査概説_学習教材 |
○:お振込・クレジットカード払いが可能です。
○:請求書・領収書の発行は簡単ダウンロード!
→インボイス制度に基づく適格請求書発行事業者の登録番号も記載しています。
○:お得なキャンペーン情報などは本記事トップをご確認ください。
ラインバランスとは何?
ラインバランスとは、生産ラインにおいて各工程の作業時間を均等に保つことを指します。生産ラインがスムーズに稼働するためには、すべての工程が同じペースで進行することが理想です。
ラインバランス | 意味 |
良い | 生産効率が高まり、無駄な待ち時間や在庫の滞留が減少します。 |
悪い | 特定の工程での滞留や遅延が発生し、全体の生産性が低下します。 |
以上より、ラインバランスを保つことは、製造業における重要な課題の一つです。
ボトルネック工程の特定方法
生産ラインの効率を最大化するためには、ラインバランスを計算し、ボトルネック工程を特定することが重要です。まず、各工程の作業時間を計測し、ライン全体の作業時間を合計します。その後、各工程の平均作業時間を計算し、以下の計算式を使用してラインバランスを求めます。
ラインバランス(%)=(総作業時間/(最大工程時間×工程数))×100
具体的な例を挙げると、各工程の作業時間がそれぞれ10分、12分、8分、15分で、全体の作業時間が45分、最大工程時間が15分、工程数が4つの場合、ラインバランスは次のように計算されます。
この計算結果から、最も作業時間の長い工程(この場合は15分)がボトルネック工程となります。ボトルネック工程は、生産ライン全体の流れを阻害し、効率を低下させる原因となります。具体的には、他の工程がボトルネック工程を待つ間に停滞し、結果として生産全体の遅延や在庫の増加を引き起こします。
ボトルネック工程を特定することは、生産ラインの改善において非常に重要です。特定されたボトルネックを解消することで、全体の生産効率を向上させることができます。
例えば、ボトルネック工程の作業方法を見直す、追加のリソースを投入する、または工程自体を再設計するなどの手法が考えられます。これにより、生産ライン全体の流れがスムーズになり、効率的な生産が実現できます。
関連記事
ボトルネック工程の改善手法
改善項目 | 対策 |
工程作業の分割と結合 | 時間がかかる工程を分割し、それぞれを異なる作業者に割り当てること。また前後の工程で時間が短い作業があれば、それらを結合し、一つの工程にする。 |
人数調整 | ボトルネック工程に追加の作業者を配置することで、その工程の処理能力を向上させ、全体のバランスを取る。 |
スキル再配分 | 難易度の高い工程には経験豊富な作業者を配置し、簡単な工程には新人を配置するなど。 |
作業方法の改善 | 作業手順を簡素化する、または効率的な道具を導入することで、作業時間を短縮。 |
U字ライン化 | 生産ラインをU字型に配置し、作業者が複数の工程を一貫して行えるようにすることで、移動時間の削減やスムーズな工程間の連携が実現 |
改善手法の具体的な実施例
例えば、ある製造業では、ネック工程の分割と結合を行うことで、生産効率が20%向上しました。また、作業者の人数調整により、特定の工程の待ち時間が50%削減されました。さらに、スキルベースの再配分により、全体の生産時間が15%短縮されました。
他の事例では、ある自動車部品メーカーでは、U字ライン化を導入し、全体の生産効率が30%向上しました。また、作業方法の見直しにより、品質向上とコスト削減を同時に実現したケースもあります。
これらの成功事例を参考にすることで、自社の生産ラインにも適用できる改善手法が見つかるでしょう。
関連記事
ラインバランス:まとめ
ラインバランスの維持とボトルネック工程の改善は、製造業において生産効率を最大化するための重要な課題です。ラインバランスとは各工程の作業時間を均等に保つことであり、これが崩れると生産性の低下やコスト増加を招きます。
ボトルネック工程を特定し、改善することで全体の生産効率が向上します。具体的な改善手法として、工程作業の分割・結合、作業者の人数調整、スキルに基づく再配分、作業方法の見直し、多工程持ちU字ライン化があります。これらの手法を実践することで、生産ラインの最適化が図れます。
成功事例も多く、効率化と品質向上を同時に実現することが可能です。継続的な改善を通じて、競争力のある生産体制を築いていきましょう。

【このサービスが人気の理由】 ①:本当に必要な部分だけを相談できるから、コスパが抜群 ②:難しい要求事項も、実際の現場に合わせたわかりやすい説明がもらえるから ③:初めてでも安心!専門用語をかみ砕いた、丁寧なサポートが受けられるから |
【サービスの特徴】
品質マネジメントの悩みは、お気軽にご相談ください。IATF16949・ISO9001・VDA6.3に精通した専門家が、メールで丁寧にお応えします。「これって聞いていいのかな?」という疑問も、まずは1回お試しください。初回は無料。1質問から気軽に使えるから、コンサル契約前の“確認用”としても最適です。
お客様からいただいたお声はこちら
相談内容:3つの約束
IATF16949・ISO9001・VDA6.3に関する疑問や実務の悩みに対応しています。
要求事項の意味を分かりやすく解説し、現場での実践につながるポイントまで丁寧にお伝えします。
審査対応や文書作成、FMEA・CPの見直し、品質目標やKPI設定など、幅広いテーマに対応可能です。
「この質問はしていいのかな?」と悩む前に、まずはお気軽にご相談ください!
お問い合わせページはこちら