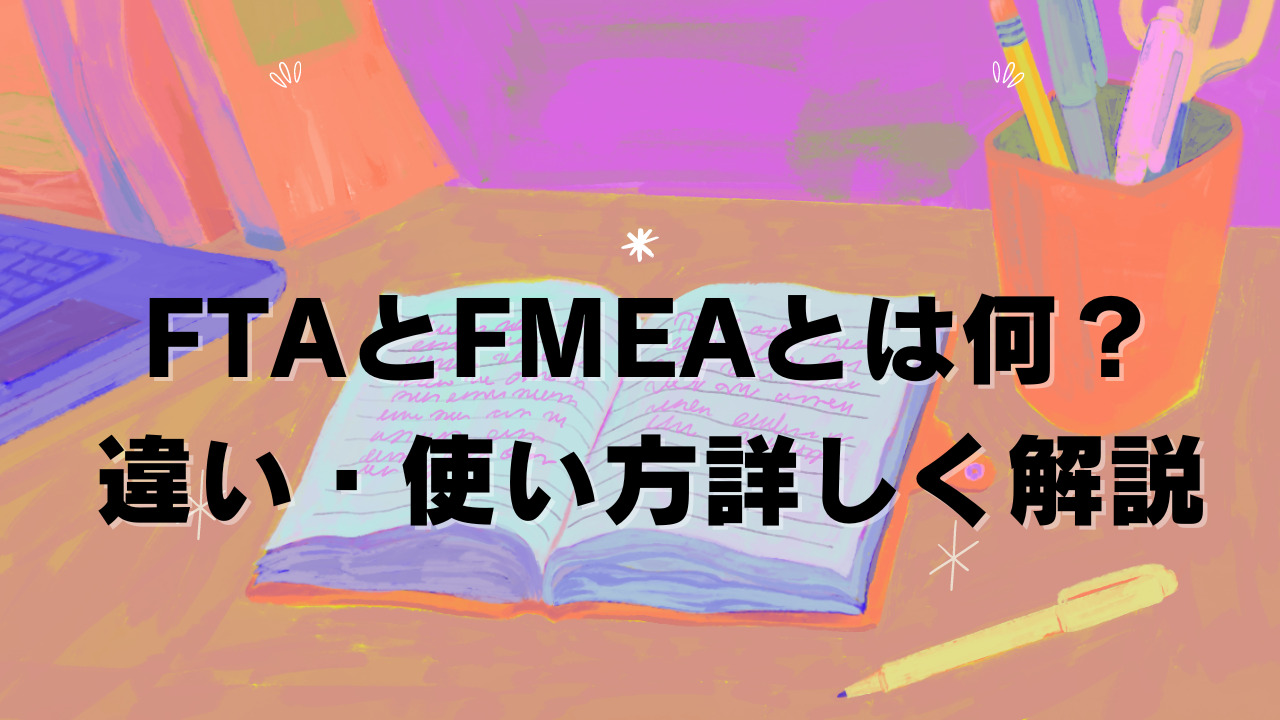
自動車業界のみならず、製造業に従事さえている方であれば一度は耳にしたことがあるFTAとFMEA。これらのツールは使用方法が難しく、ほとんどは顧客要望があるから対応しているといったメーカーさんが多いと思います。
しかしこの二つのツールは、使い方は難しくなく、使用方法を理解すれば品質向上に大きく貢献するツールとなっておりますので、是非その使い方の違いについてご理解いただければ幸いです。
品質マネジメントシステム普及の応援が目的のサイトです!「難解な規格を簡単に解説」をモットーに、「ちょっと相談したい」ときに頼りになるコンサルタントを目指しています!まずはお気軽にご連絡ください★
「無料で学ぶ」「有料で実践する」——皆様の目的に合わせて活用可能です!
✅ QMS・品質管理・製造ノウハウを無料で学びたい方へ
👉 本サイト「QMS学習支援サイト」を活用しましょう!「QMSについて知りたい」「品質管理の基礎を学びたい」方に最適!
✔ IATF 16949やISO 9001・VDA6.3の基礎を学ぶ
✔ 品質管理や製造ノウハウを無料で読む
✔ 実務に役立つ情報を定期的にチェック
✅ 実践的なツールやサポートが欲しい方へ
👉 姉妹サイト「QMS認証パートナー」では、実務で使える有料のサポートサービスを提供!「すぐに使える資料が欲しい」「専門家のサポートが必要」な方に最適!
✔ コンサルティングで具体的な課題を解決
✔ すぐに使える帳票や規定のサンプルを購入
✔ より実践的な学習教材でスキルアップ
皆様の目的に合わせて活用可能です!
・当サイトの内容は、あくまでもコンサルタントとして経験による見解です。そのため、保証するものではございません。 ・各規格の原文はありません。また、規格番号や題目なども当社の解釈です。 ・各規格については、規格公式サイトを必ず確認してください。 ・メールコンサルティングは空きあります(2025年6月現在)。この機会に「ちょっと相談」してみませんか?1週間の無料サービス期間を是非ご利用ください。 →サービスのお問い合わせはこちら |
2025年:新企画始動告知!
メールコンサルティング初回契約:初月50%以上割引★
サービス詳細はこちら
・オンラインコンサル/現地コンサルの空き状況について
【現在の空き状況:2025年6月現在】
・平日:6時間以上ご利用で月1回のみ
・夜間:19:30-21:00でご相談承ります
・土日:少々空きあります
オンライン会議システムを利用したコンサル詳細はこちら
【メールコンサルティングのご案内】
✅文書作成はできたけど、これで審査に通るのか不安…
✅教科書やネットの情報通りに進めてきたけど、現場に合っていない気がする…
✅現地コンサルタントと契約して聞きたいけど、何十万円も払うのはちょっと…
そんな悩みをお持ちの方に向けたのが、「IATF・ISO専門のメールコンサルティング」です。全国の大手企業様、中小企業様の支援実績を持つQMS認証パートナーが、個別で具体的なアドバイスを“メールで”お届けします。Zoomや訪問と違って、気軽に相談できるうえ、記録が残るから安心。初回相談は無料です。
この記事の目次
FTAとは何か?その概念と用途を解説
FTA(Fault Tree Analysis:フォールトツリー解析)は、システムやプロセスにおける失敗や不具合の原因を体系的に分析するための手法です。この手法は、特にリスク分析や安全性の評価において重要な役割を果たします。その概要や用途について、以下で詳しく説明します。
FTAの概念と基礎
FTAの基本的な目的は、「失敗が発生する可能性のある特定の出来事(トップイベント)」を明確にし、その出来事の原因となる要素を視覚的に示すことです。この視覚化はロジックツリー形式で行われ、原因の相互関係や構造が一目でわかるように整理されます。
システム全体に重大な影響を与える故障や失敗のことで、例えば航空機のエンジン停止、データベースシステムのダウン、工場設備の重大事故などが該当します。
FTAでは、このトップイベントが発生する原因を特定し、それを防ぐための対策を講じる基盤を構築します。
FTAの用途と特に有用な場面
FTAは、以下のような場面で幅広く活用されます。
システムやプロセスの故障原因の分析
システムの故障がどのような要因で引き起こされるのかを、詳細に把握するために用いられます。例えば、複数の部品や工程が絡み合う製造プロセスで、どの部分がトラブルの原因となる可能性が高いかを明らかにするために役立ちます。
確率論を用いたリスク評価
各要素の故障確率を計算し、それらが連鎖的にトップイベントにつながる全体のリスクを定量化します。これにより、リスクの大きさを具体的な数値で示すことができ、意思決定に必要なデータを提供します。
ミッションクリティカルシステムの設計とテスト
航空機、宇宙船、原子力発電所など、システムの失敗が重大な影響を及ぼす分野では、安全性を高めるためにFTAが必須のプロセスとされています。FTAを通じて、システムの設計段階で潜在的なリスクを特定し、それを防ぐための冗長性や安全装置を組み込むことができます。
フォールトモデルの作成
故障が発生するメカニズムを記述したモデルを構築する際、FTAを利用して原因と結果の関係を整理します。これにより、今後の類似した問題の解決や未然防止に役立てることが可能です。
ソフトウェアの安全性確保
特に自動運転車や医療機器のように、人命に関わるシステムでは、ソフトウェアに潜むバグや故障のリスクを事前に分析するためのツールとしてFTAが活用されます。
FTAのプロセスと視覚化
FTAの特徴的な部分は、「ツリー構造」で原因を示す点です。ツリーの頂点にトップイベントを置き、そこから枝分かれする形で、それに関連する個別の要因を記載します。そして、これらの要因の組み合わせを示す際に、論理演算(ANDゲートやORゲート)が使用されます。
ANDゲート:すべての要因が同時に発生した場合にトップイベントが引き起こされることを示します。
ORゲート:いずれかの要因が発生すればトップイベントが引き起こされることを示します。
こうした視覚化により、システムの全体像を把握しやすくなると同時に、どの要因がクリティカルかを見極めることが可能です。
FTA作成ステップ
FTA(Fault Tree Analysis:フォールトツリー解析)を効果的に実施するためには、いくつかのステップを順に進める必要がありますので、以下に各ステップの目的や具体的な内容を詳細に説明します。
1.トップイベントの特定
FTAの出発点は、「トップイベント」と呼ばれる特定の失敗シナリオを定義することです。トップイベントとは、システムやプロセスにおける重大な失敗や望ましくない結果を指します。例えば、発電所の運転停止、飛行機のエンジン故障、あるいはデータセンターの全システムダウンなどが該当します。
このステップでは、失敗がシステム全体にどのような影響を与えるかを明確にし、トップイベントの発生条件を具体化します。この定義が不明確であると、後続の分析が無駄になる可能性があるため、慎重に取り組む必要があります。
2.フォールトツリーの作成
トップイベントを定義した後、その発生原因を探るためにフォールトツリーを作成します。フォールトツリーは、トップイベントをツリーの頂点(ルート)に置き、その下に枝分かれする形で原因となる要素や条件を追加していく視覚的な構造です。
フォールトツリーでは、原因がどのようにトップイベントに結びつくかを示すために、ANDゲートやORゲートなどの論理記号を使用します。
・ANDゲート:すべての要因が同時に発生した場合にトップイベントが引き起こされる。
・ORゲート:いずれかの要因が発生すればトップイベントが引き起こされる。
このステップでは、個々の要因がシステム全体にどのように影響を与えるかを俯瞰的に理解することが可能になります。
3.フォールトセットの特定
フォールトツリーが完成したら、次に行うのは「フォールトセット」の特定です。フォールトセットとは、トップイベントを引き起こす可能性のあるフォールトの組み合わせを指します。この分析により、どの要因や組み合わせが問題を引き起こしやすいのかが明確になります。
例えば、特定のセンサーの故障とソフトウェアエラーが同時に発生するとトップイベントに至る場合、それぞれの要素とその関連性を詳細に調査します。この作業を通じて、クリティカルなフォールトが浮き彫りになります。
4.失敗モードの分析
フォールトセットを特定したら、それぞれのフォールトが発生する理由をさらに深く掘り下げます。このプロセスを「失敗モードの分析」と呼ばれています。具体的には、以下の項目を評価します。
故障確率:各フォールトがどの程度の頻度で発生するか。
故障影響度:フォールトが発生した場合に、システム全体にどの程度の影響を与えるか。
故障発生頻度:フォールトの原因となる要因がどれほど頻繁に発生するか。
このステップでは、統計データや過去の記録を使用して、各フォールトの影響を具体的に測定します。これにより、フォールトごとの重要性を把握することができます。
5.リスクの評価
最後のステップでは、システム全体のリスクを評価し、どのリスクが最も重要であるかを特定します。この評価には、一般的に「リスク優先度番号(RPN:Risk Priority Number)」が使用されます。RPNは、以下の3つの要素を掛け合わせて算出されます。
発生確率:フォールトが発生する可能性。
影響度:フォールトがシステム全体に与える影響。
検出可能性:フォールトが発生した際、それをどの程度早く検出できるか。
RPNが高い項目は、優先的に対策を講じるべきリスクとして扱われます。この評価結果を基に、必要な設計変更や運用手順の改善を行うことで、システムの安全性を向上させることが可能です。
QMS認証パートナーの人気サービスのご紹介
📩 QMSメール相談サービス
サービスの詳細はこちら
ISO9001・IATF16949・VDA6.3に関するちょっとした疑問や不安。「誰かに聞けたらすぐ解決するのに…」と感じたことはありませんか?
そんな現場の声に応える「質問1回から使える専門相談サービス」です。
面談不要、メールだけで完結。
初回は無料で1回質問OKなので安心
月額プラン(サブスク形式)なら何度でも安心相談!
→審査直前の駆け込み対応や、日々の運用相談もまとめてサポートいたします。
FMEAとは何か?その概念と用途を解説
FMEAは、特定の製品やプロセスがどのように失敗する可能性があるか(失敗モード)を分析し、その失敗が引き起こす影響や原因を明らかにします。この情報をもとに、潜在的なリスクを減少させるための対策を立案します。
この手法は、FTA(フォールトツリー解析)と似ていますが、予防に焦点を当てており、具体的には次の3つの要素を特定します。
失敗モード
どのような形で製品やプロセスが機能しなくなるか、または期待される性能を満たさないかを特定します。例えば、機械部品の破損、ソフトウェアの誤作動、材料の劣化などが挙げられます。
失敗の影響
各失敗モードがシステム全体やユーザーにどのような影響を及ぼすかを評価します。たとえば、車のブレーキシステムが故障すれば安全性に重大な影響を及ぼします。
失敗の原因
失敗モードが発生する背後の原因を分析します。設計の不備、製造工程のミス、材料の選択ミス、操作エラーなど、さまざまな要因が該当します。
FMEAの用途
FMEAは、リスク管理や品質管理の手法として広く用いられており、以下のような具体的な場面で活用されます。
1.プロダクトライフサイクル全体での失敗の予防
製品の設計から製造、使用、廃棄に至るまでのライフサイクル全体を通じて潜在的な失敗を予測し、適切な予防策を講じるためにFMEAが活用されます。これにより、製品の信頼性が向上し、顧客満足度が高まります。
2.フェイルセーフ設計の改善
フェイルセーフとは、万が一の失敗が発生した場合でも、安全性を確保するための設計方針を指します。FMEAを用いることで、失敗モードとその影響を明らかにし、安全な設計(例:冗長性の追加や自動停止機能の導入)を構築することが可能です。
3.リリアビリティエンジニアリングの推進
リリアビリティエンジニアリング(信頼性工学)は、製品やプロセスが計画通りに動作し続ける能力を向上させる分野です。FMEAを活用して、信頼性を損なう可能性のある要素を洗い出し、問題を未然に防ぐための改良を行います。
4.設計プロセスの強化
製品やプロセスの設計段階において、FMEAを実施することで潜在的な問題を特定し、設計変更を行うことで完成度を高めます。これにより、開発後期や運用開始後に発生する修正コストを大幅に削減することができます。
5.テストプランの最適化
FMEAを通じて、失敗が発生する可能性の高い箇所を特定することで、テスト計画を効率的に設計することが可能です。テスト対象や手法を最適化することで、無駄を削減しながら品質保証を強化します。
FMEAの基本的なステップ
FMEA(Failure Mode and Effects Analysis:失敗モード及び効果分析)は、製品やプロセスのリスクを体系的に評価し、潜在的な問題を予防するための手法です。その実施には、以下のようなステップが含まれます。それぞれのステップを詳しく説明します。
1.プロセスフローチャートの作成
最初のステップは、分析対象のプロセス全体を視覚的に表現することです。プロセスフローチャートを用いて、各工程やステップがどのように連携しているかを明確に示します。これにより、プロセスの全体像を把握し、次に分析すべき具体的な部分を特定しやすくなります。
例として、製造工程の場合、原材料の受け入れから最終製品の出荷までの流れをフローチャートに描きます。このフローチャートは、後続の分析で各工程を検討するための基盤となります。
2.失敗モードの特定
次に、プロセス内の各ステップにおいて、どのような失敗が発生する可能性があるかを考えます。これを「失敗モード」と呼びます。失敗モードとは、システムやプロセスが期待どおりに機能しない具体的な形態を指します。
例えば、製造工程では「部品の寸法が規格外になる」「接合が不完全」「誤った部品が使用される」などが失敗モードとして挙げられます。このステップでは、あらゆる可能性をリストアップすることが重要です。
3.失敗の影響の特定
次に、各失敗モードが引き起こす可能性のある結果や影響を評価します。このステップでは、失敗がシステム全体、顧客、またはユーザーにどのような影響を及ぼすかを検討します。
例えば、自動車のブレーキシステムで「ブレーキが作動しない」という失敗モードが発生した場合、その影響は「運転者の安全が危険にさらされる」「車両の制御が失われる」といった重大な結果に直結します。このような影響の評価は、リスクの重要性を判断するために不可欠です。
4.失敗の原因の特定
失敗モードが特定されたら、その失敗が発生する原因を探求します。失敗の原因は、設計上の問題、材料の欠陥、製造工程の不備、操作ミスなど多岐にわたります。この段階では、根本原因を明確にすることが目的です。
例えば、「部品が寸法外になる」という失敗モードの原因として、「製造装置のキャリブレーションミス」「作業者のスキル不足」「不適切な素材の使用」などが挙げられるかもしれません。原因を明確にすることで、効果的な対策を講じる基盤が得られます。
5.リスクの評価
失敗モードの影響と原因を特定したら、次にそのリスクを評価します。このステップでは、以下の3つの要素を考慮してリスクを定量化します:
故障確率(Occurrence:O)
失敗モードがどれくらいの頻度で発生するかを評価します。
故障影響度(Severity:S)
失敗モードが発生した場合の影響の重大度を評価します。
検出可能性(Detection:D)
失敗モードが発生する前または発生後に、それを検出できる可能性を評価します。
これらの値を掛け合わせることで、リスク優先度番号(RPN:Risk Priority Number)が計算されます。計算式は、「RPN=O×S×D」であらわされ、RPNが高いほど、リスクが大きいことを示します。これにより、どの失敗モードが最も緊急に対処すべきかが分かります。
6.改善計画の作成
最後に、リスクが高い失敗モードに対するアクションプランを作成します。このステップでは、RPNを低減させるための具体的な対策を立案し、それを実施します。対策には、以下のような方法が含まれます。
①設計変更を行い、失敗モードの原因を除去する。
②製造工程を改善して、失敗の発生確率を下げる。
③検査工程を追加して、失敗の検出可能性を高める。
これらの改善計画は、リスクを低減するだけでなく、製品やプロセス全体の品質向上にも寄与します。
FTAとFMEAの違い
FTAとFMEAは両方ともリスクを評価し、失敗を理解するための強力なツールですが、それぞれ異なる方法でこれを行います。
FTAはシステムのトップレベルから考え、特定のトップイベントが発生するためのシーケンス分析を行い、それが発生するためのフォールトセットを特定します。
対してFMEAは、個々のコンポーネントやプロセスのレベルで考え、可能な失敗モードを特定し、その影響と原因を評価します。
FTAは、一般的には、より広範で複雑なシステムのリスク評価に用いられます。特に、確率的リスク評価や原因と結果の分析を必要とする複雑なシステムには適しています。
一方、FMEAは製品設計や製造プロセスの早期段階で、潜在的な問題を特定し、予防保全を促進するために使用されます。FMEAは、故障確率、故障影響度、故障発生頻度といった要素を考慮して、リスクを定量化します。
FTAとFMEAの効果的な使い方:まとめ
FTAとFMEAは、リスク管理や品質向上のための強力な手法です。
FTAは、システムやプロセスの重大な失敗(トップイベント)の原因を論理ツリーで特定し、リスクを予防・軽減するのに適しています。
一方、FMEAは、個々の失敗モードを分析し、影響・原因を明らかにしてリスク優先度を評価することで、設計や運用段階での問題を防ぎます。FTAはシステム全体の失敗要因の俯瞰に、FMEAは詳細なリスク評価と改善計画の作成に適しており、目的や状況に応じた使い分けが重要です。
両方とても重要なツールなので、是非貴社でも役に立ててくださいね!

【このサービスが人気の理由】 ①:本当に必要な部分だけを相談できるから、コスパが抜群 ②:難しい要求事項も、実際の現場に合わせたわかりやすい説明がもらえるから ③:初めてでも安心!専門用語をかみ砕いた、丁寧なサポートが受けられるから |
【サービスの特徴】
品質マネジメントの悩みは、お気軽にご相談ください。IATF16949・ISO9001・VDA6.3に精通した専門家が、メールで丁寧にお応えします。「これって聞いていいのかな?」という疑問も、まずは1回お試しください。初回は無料。1質問から気軽に使えるから、コンサル契約前の“確認用”としても最適です。
お客様からいただいたお声はこちら
相談内容:3つの約束
IATF16949・ISO9001・VDA6.3に関する疑問や実務の悩みに対応しています。
要求事項の意味を分かりやすく解説し、現場での実践につながるポイントまで丁寧にお伝えします。
審査対応や文書作成、FMEA・CPの見直し、品質目標やKPI設定など、幅広いテーマに対応可能です。
「この質問はしていいのかな?」と悩む前に、まずはお気軽にご相談ください!
お問い合わせページはこちら