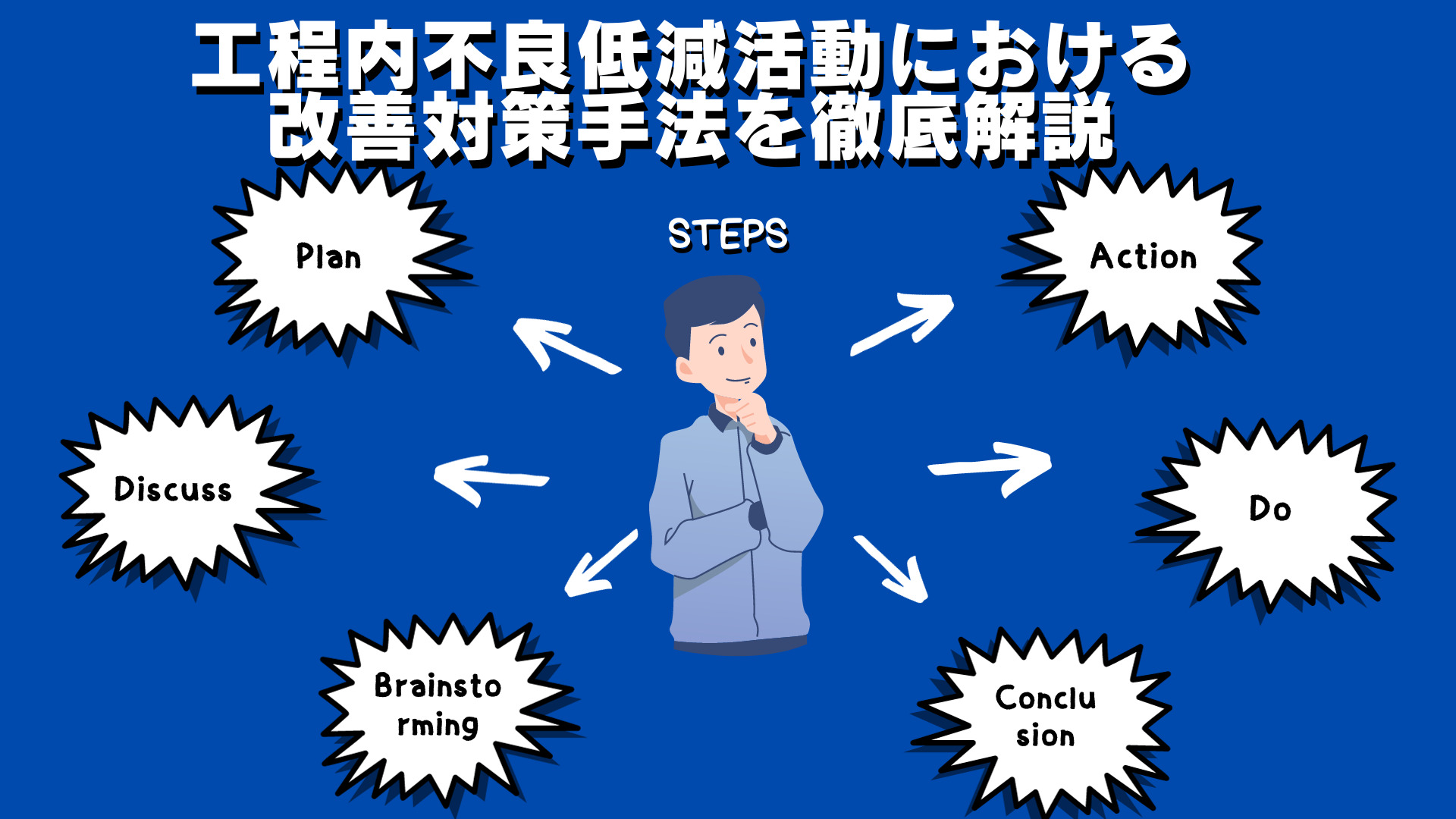
製造業における工程内不良の低減は、企業の生産性と品質向上に直結する重要な課題です。本記事では、工程内不良が発生する原因や、改善活動がうまく進まない理由を解説し、効果的な改善・対策手法を7つ紹介しています。
品質マネジメントの要素を取り入れた実践的なアプローチを通じて、組織全体で持続的な品質向上を目指すための参考になれば幸いです。
品質マネジメントシステム普及の応援が目的のサイトです!「難解な規格を簡単に解説」をモットーに、「ちょっと相談したい」ときに頼りになるコンサルタントを目指しています!まずはお気軽にご連絡ください★
「無料で学ぶ」「有料で実践する」——皆様の目的に合わせて活用可能です!
✅ QMS・品質管理・製造ノウハウを無料で学びたい方へ
👉 本サイト「QMS学習支援サイト」を活用しましょう!「QMSについて知りたい」「品質管理の基礎を学びたい」方に最適!
✔ IATF 16949やISO 9001・VDA6.3の基礎を学ぶ
✔ 品質管理や製造ノウハウを無料で読む
✔ 実務に役立つ情報を定期的にチェック
✅ 実践的なツールやサポートが欲しい方へ
👉 姉妹サイト「QMS認証パートナー」では、実務で使える有料のサポートサービスを提供!「すぐに使える資料が欲しい」「専門家のサポートが必要」な方に最適!
✔ コンサルティングで具体的な課題を解決
✔ すぐに使える帳票や規定のサンプルを購入
✔ より実践的な学習教材でスキルアップ
皆様の目的に合わせて活用可能です!
・当サイトの内容は、あくまでもコンサルタントとして経験による見解です。そのため、保証するものではございません。 ・各規格の原文はありません。また、規格番号や題目なども当社の解釈です。 ・各規格については、規格公式サイトを必ず確認してください。 ・メールコンサルティングは空きあります(2025年6月現在)。この機会に「ちょっと相談」してみませんか?1週間の無料サービス期間を是非ご利用ください。 →サービスのお問い合わせはこちら |
2025年:新企画始動告知!
メールコンサルティング初回契約:初月50%以上割引★
サービス詳細はこちら
・オンラインコンサル/現地コンサルの空き状況について
【現在の空き状況:2025年6月現在】
・平日:6時間以上ご利用で月1回のみ
・夜間:19:30-21:00でご相談承ります
・土日:少々空きあります
オンライン会議システムを利用したコンサル詳細はこちら
ISO9001の構築・運用のコツは「規格の理解」と「ルールと記録の構築」の2つがカギ!教材とサンプルを利用しつつ、相談しながら低コストで対応可能なノウハウをご提供いたします!
【ISO9001:おすすめ教材】
👑 | 教材No. | タイトル:詳細はこちら |
1 | No.3-001 | ISO9001学習支援教材 |
2 | No.9121 | 顧客満足度調査表 |
3 | No.72-1 | 個人の力量と目標管理シート |
○:お振込・クレジットカード払いが可能です。
○:請求書・領収書の発行は簡単ダウンロード!
→インボイス制度に基づく適格請求書発行事業者の登録番号も記載しています。
○:お得なキャンペーン情報などは本記事トップをご確認ください。
この記事の目次
工程内不良とは何か
工程内不良とは、製造過程において発生する品質の問題を指し、具体的には、部品の組み付けミスや加工不足、塗装ムラ、電気的な異常などが挙げられます。
これらの不良が蓄積されると、製品全体の品質に悪影響を及ぼし、結果として顧客からのクレームや返品、さらには修理が必要になるケースも増えます。
工程内不良は、製品の信頼性を損なう大きな要因となり、企業のブランドイメージや市場での競争力にも影響を与えるため、迅速かつ的確な対策が求められます。
工程内不良がなぜ起きるのか
工程内不良が発生する主な原因として、設計ミスや部品の品質不良、操作ミス、設備の老朽化、さらには教育の不足などが挙げられます。
例えば、部品を供給する業者の品質管理が不十分であったり、オペレーターの技術や知識が不足していたり、機械設備のメンテナンスが適切に行われていない場合、不良が生じやすくなります。
これらの問題を根本的に解決するためには、各工程での品質管理体制を強化し、問題の発生を未然に防ぐ仕組みを構築することが不可欠です。
工程内不良改善活動が上手くいかない原因
多くの製造業が工程内不良の改善活動に取り組んでいるものの、成功に至らないケースも少なくありません。その背景にはいくつかの原因が考えられます。
まず、真の原因を特定することが難しく、問題の根本にたどり着けないことが挙げられます。また、改善策の立案や実行が不十分であったり、計画が中途半端に終わってしまうことも失敗の要因です。
さらに、改善活動の継続性が欠如している場合も多く、初期の改善が見られても、その後のフォローやモニタリングが不十分なために、効果が持続しないこともあります。
QMS認証パートナーの人気サービスのご紹介
📩 QMSメール相談サービス
サービスの詳細はこちら
ISO9001・IATF16949・VDA6.3に関するちょっとした疑問や不安。「誰かに聞けたらすぐ解決するのに…」と感じたことはありませんか?
そんな現場の声に応える「質問1回から使える専門相談サービス」です。
面談不要、メールだけで完結。
初回は無料で1回質問OKなので安心
月額プラン(サブスク形式)なら何度でも安心相談!
→審査直前の駆け込み対応や、日々の運用相談もまとめてサポートいたします。
工程内不良改善・対策で重要な要素8選
①製品設計段階で市場クレーム過去トラをインプット!
製品設計の段階で、過去に発生した市場クレームや不具合情報を考慮に入れることは、製品の品質を高めるうえで非常に重要です。実際に市場で使用された製品からのフィードバックは、設計者や開発者が予期しない実際の使用状況や問題点を明らかにします。
そのため、これらの情報を設計の初期段階で取り入れることで、製品の信頼性や耐久性を向上させることができます。また、顧客のニーズや要求を満たすためには、実際の声を取り入れることが不可欠です。
これにより、製品の市場での受け入れや評価を高めることができ、長期的にはブランドの信頼性やリピート購入率を向上させることにつながります。
関連記事
②工程設計段階で工程過去トラをインプット!
工程設計の段階で、過去の工程で発生した不具合やトラブル情報を取り入れることで、新たな工程の品質向上につなげることができます。
過去のトラブルや不具合は、それ自体が価値あるデータであり、それを活用しない手はありません。
実際の生産現場で発生した問題を知ることで、それを防ぐための新たな工程や手法を考案することが可能となります。
例えば、ある部品の取り付けが難しいというフィードバックがあった場合、その部品の形状を変更する、または取り付け工具を改良することで、工程内での不具合を低減することができます。
関連記事
③生産工程毎に「品質目標値」を設定!
製造工程ごとに品質目標値を設定することは、品質向上のための具体的な指針を提供します。具体的な数値目標を持つことで、オペレーターや品質管理担当者はその目標を達成するための努力を強化することができます。
また、目標値が明確であることで、進捗のモニタリングや評価も容易になります。
このような数値目標は、組織内でのコミュニケーションや意識統一のツールとしても有効です。
定期的なミーティングやレビューを通じて、目標達成のための取り組みや問題点を共有することで、組織全体の品質向上を促進することができます。
関連記事
④発生した問題は「真の原因」を追究する!
工程内で発生した問題に対して、その表面的な原因だけでなく、真の原因を追求することは、繰り返し同じ問題が発生することを防ぐ上で非常に重要です。
例えば、ある機械が頻繁に故障するという問題が発生した場合、その原因が機械の老朽化であるのか、オペレーターの操作ミスであるのか、または外部からの何らかの影響であるのかを明確にすることで、適切な対策を講じることができます。
真の原因を特定するためには、詳細なデータの収集や分析、関連する人々とのコミュニケーションが不可欠です。
また、真の原因を追求するプロセスは、組織内の問題解決能力を高めることにも寄与します。
継続的に真の原因を特定し、それに基づく対策を実施することで、組織全体としての問題解決のスキルや知識が蓄積され、未来の似たような問題にも迅速かつ適切に対応することが可能となります。
関連記事
⑤改善対策は「有効性」を評価!
ある問題に対して改善対策を実施した後、その効果を定期的に評価することは、持続的な品質向上のために欠かせないステップです。
有効性の評価を行うことで、実施した対策が目的を達成しているか、またはさらなる改善が必要かを明確にすることができます。
特に、新しい手法や技術を導入した場合、期待される効果が得られているかを確認することは重要です。
この評価を通じて、次回の問題解決や改善活動に生かすための知見や経験を蓄積することができます。
関連記事
⑥類似工程には「水平展開」を確実に行う!
一つの工程で得られた成功体験や知見を、類似する他の工程にも展開することで、組織全体の品質向上を実現することができます。
これにより、各工程が同じ問題に対して独自に対策を考案する手間を省き、組織全体としての効率を向上させることができます。
また、組織内でのベストプラクティスの共有や、異なる部門やチーム間でのコミュニケーションを促進することで、組織の学習能力や知識の蓄積を加速することが可能となります。
⑦最低半年に1回「工程監査」を実施する!
定期的な工程監査は、工程の品質管理が適切に行われているかを客観的に評価するための重要な手段です。
外部や内部の専門家による監査を通じて、潜在的な問題点やリスクを早期に特定し、予防的な対策を講じることができます。
また、監査の結果をもとに、組織内での品質管理のスタンダードやガイドラインを見直し、絶えず品質管理のレベルを向上させることが可能となります。
関連記事
⑧必要に応じて自社の「品質マネジメントシステム」を見直す!
品質マネジメントシステムは、製造業における品質を継続的に向上させるための体系的な取り組みを意味します。
しかしこのシステムは、一度設定したからといって永遠に適切であるとは限りません。
市場のニーズ、生産技術、社内の人材や組織構造の変動など、多岐にわたる要因が影響します。そのため、定期的な見直しと更新は必須です。
具体的には、新しい技術の導入や変更時、市場からの大きなクレーム、新しい規制や法令の変更などの際には、品質マネジメントシステムの見直しを行うことが求められます。
また、各工程の監査結果や品質データをもとに、改善点や課題を特定し、システム全体の見直しを進めることで、より効果的な品質マネジメントを実現することができます。
関連記事
不適合・異常対応用教材のご紹介
帳票名 | 不適合)異常品改善対策書 | ||
---|---|---|---|
納品形式 | ダウンロード | ||
ファイル形式 | Excel:貴社にて自由にカスタマイズ可能です | ||
特徴 | 品質問題を迅速解決!異常品質改善対策書と不適合品処理管理規定で、的確な対応と再発防止を徹底サポート。現場の品質向上・IATF16949対応とISO9001構築・運用に最適なツールです! | ||
詳細 | 商品詳細はこちら | ||
関連規定 | No.8710_不適合品処理管理規定 |
工程内不良低減活動の改善・対策:まとめ
製造業における工程内不良の低減は、組織全体の生産性や品質を向上させる重要な要素です。本記事では、工程内不良の原因や改善活動が上手くいかない理由を探るとともに、効果的な改善・対策の手法を7つ紹介しました。
品質を向上させるための取り組みは、単なる技術や手法の導入だけではなく、組織文化やマインドセットの変革も伴う必要があります。日々の業務の中で、真の原因を追求し、持続的な改善を目指す姿勢を育てることが、真の品質向上を実現するための鍵となります。
この記事が、製造業に従事する皆様の工程内不良低減活動の参考となり、より質の高い製品の製造に役立てられることを心より願っています。

【このサービスが人気の理由】 ①:本当に必要な部分だけを相談できるから、コスパが抜群 ②:難しい要求事項も、実際の現場に合わせたわかりやすい説明がもらえるから ③:初めてでも安心!専門用語をかみ砕いた、丁寧なサポートが受けられるから |
【サービスの特徴】
品質マネジメントの悩みは、お気軽にご相談ください。IATF16949・ISO9001・VDA6.3に精通した専門家が、メールで丁寧にお応えします。「これって聞いていいのかな?」という疑問も、まずは1回お試しください。初回は無料。1質問から気軽に使えるから、コンサル契約前の“確認用”としても最適です。
お客様からいただいたお声はこちら
相談内容:3つの約束
IATF16949・ISO9001・VDA6.3に関する疑問や実務の悩みに対応しています。
要求事項の意味を分かりやすく解説し、現場での実践につながるポイントまで丁寧にお伝えします。
審査対応や文書作成、FMEA・CPの見直し、品質目標やKPI設定など、幅広いテーマに対応可能です。
「この質問はしていいのかな?」と悩む前に、まずはお気軽にご相談ください!
お問い合わせページはこちら